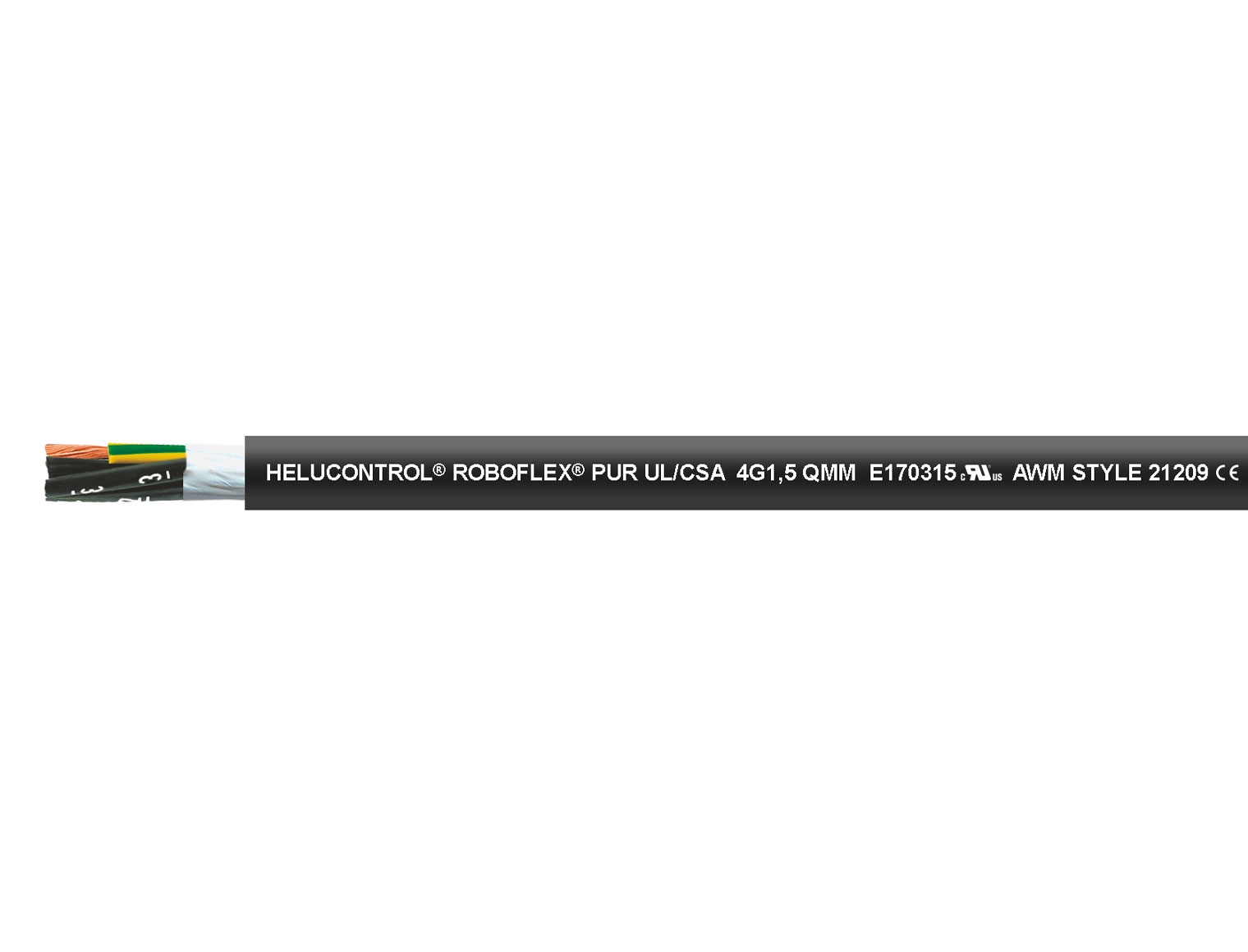
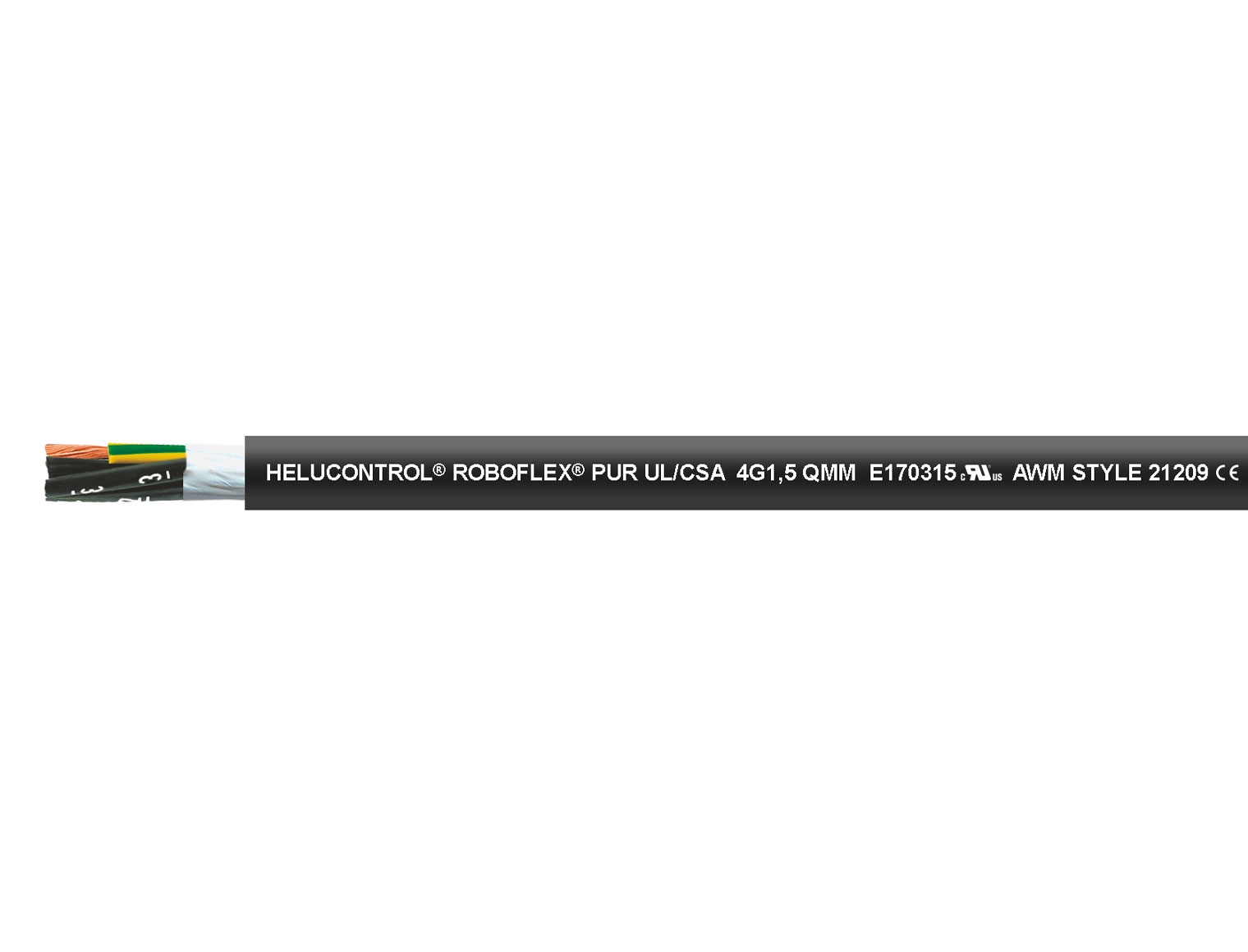
HELUCONTROL® ROBOFLEX® PUR UL/CSA black 25 G 1.5 mm²
Part no. 11023004
- PUR robot cable
- UL Style 21209 / 600 V
- Temperature range up to +90°C
Item Details HELUCONTROL® ROBOFLEX® PUR UL/CSA black 25 G 1.5 mm²
- Part no.
- 11023004
- Item description
- HELUCONTROL® ROBOFLEX® PUR UL/CSA black 25 G 1.5 mm²
- AWG (approx.)
- 16
- Outer Ø mm (approx.)
- 21.4
- Cu-weight kg/km
- 379.5
- Weight kg/km (approx.)
- 628.0
- Copper base in EUR / 100 kg
- 150
- Metres per Packaging Unit
- 500, 1000
- Cut-to-length service available
- yes
- EAN / GTIN
- 4060892532634
- Customs tariff number
- 85444995
Technical Data HELUCONTROL® ROBOFLEX® PUR UL/CSA black 25 G 1.5 mm²
PUR robot cable acc. to UL-Std. 758 (AWM) Style 21209, CSA-Std. C22.2 No. 210 - AWM I/II A/B | |
Temperature range | flexible -30°C to +90°C fixed -40°C to +90°C |
Nominal voltage | VDE AC U0/U 300/500 V UL (AWM) AC 600 V |
Test voltage core/core | 2000 V |
Minimum bending radius | fixed 5x Outer-Ø flexible: see properties |
Details HELUCONTROL® ROBOFLEX® PUR UL/CSA black 25 G 1.5 mm²
Cable Structure
-
- Copper wire bare, extra finely stranded acc. to DIN VDE 0295 Class 6 / IEC 60228 Class 6
-
- Core insulation: PP
-
- Core identification acc. to DIN VDE 0293-334, black cores with consecutive labeling in white digits
-
- G = with protective conductor GN-YE,
- x = without protective conductor
-
- Stranding:
- 2 - 8 core(s): cores stranded into one layer with an optimally matched lay length
- 12 - 41 core(s): cores stranded into bundles with optimally matched lay lengths; bundles stranded together around a tensile core
-
- Fleece wrapping
-
- Outer sheath: Special grade of full polyurethane acc. to DIN VDE 0207-363-10-2 / DIN EN 50363-10-2 (compound type TMPU)
-
- Sheath colour: black (RAL 9005)
-
- Length marking: in metres
Properties
-
- resistant to: oil, UV radiation, ozone, oxygen, weathering effects, hydrolysis, microbes, coolants, hydraulic fluids, acids, alkalis, greases, seawater and wastewater
-
- highly abrasion-resistant, notch-resistant, tear-resistant, cut-resistant, wear-resistant, low adhesion
-
- smooth, high-quality core insulation for eased sliding and optimized core stranding ensure long service-life within applications that request combined bending and torsion movements
-
- for outdoor use
-
- torsion rated
-
- suitable for use in drag chains
-
- Torsion parameters
- Acceleration (max.): 60 °/s²
- Velocity (max.): 180 °/s
- Minimum bending radius: 10x Outer-Ø
- Torsional stress up to 180 °/m: 10 Mio. Cycles (max.)
- Torsional stress up to 360 °/m: 5 Mio. Cycles (max.)
-
- Drag chain parameters
- Acceleration (max.): 10 m/s²
- Velocity (max.), unsupported: 3 m/s
- Velocity (max.), gliding: 2 m/s
- Traverse path (max.): 10 m
- Minimum bending radius (Traverse path ≤ 3m): 10x Outer-Ø
- Minimum bending radius (Traverse path > 3m): 12.5x Outer-Ø
- Bending cycles (max.): 10 Mio.
-
- halogen-free
-
- the materials used during manufacturing are cadmium-free, contain no silicone and are free from substances harmful to the wetting properties of lacquers
Tests
-
- halogen-free acc. to DIN VDE 0482-754-1 / DIN EN 60754-1 / IEC 60754-1
-
- flame-retardant acc. to DIN VDE 0482-332-1-2 / DIN EN 60332-1-2 / IEC 60332-1-2, UL-VW-1, CSA FT1
-
- oil-resistant acc. to DIN VDE 0473-811-404 / DIN EN 60811-404 / IEC 60811-404
-
- UV-resistant acc. to DIN EN ISO 4892-2
-
- weather-resistant acc. to DIN EN ISO 4892-2
Notes
-
- the conductor is metrically (mm²) constructed, AWG numbers are approximated, and are for reference only
-
- for use in energy supply systems:
- 1) the assembly instructions must be observed
- 2) for special applications, we recommend contacting us and using our data entry form for energy supply systems
Application
-
- Control cable to transmit control signals specifically designed for combined torsion and bending movements; for use in assembly and welding robots, in material handlings and automation centres, in transport and conveyor systems, on rotary and swivel tables and wherever a defined cable routing with only alternating bending movements is not applicable, but 3D-movements and torsional load have an impact on the cable; for applications with the highest requirements on mechanical, chemical and thermal resilience.